Alloy Development
Design of High-Strength Aluminum Alloys for Additive Manufacturing
Currently available aluminum alloys are not able to meet all requirements for high strength, low cost, good workability, and sustainable raw material sources, because they are either adapted from the casting sector, and/or too expensive due to the use of non-sustainable elements such as for instance Scandium. To this end, a new aluminum alloy shall be developed, and meet typical mechanical and physical requirement profiles of relevant industries and be reliably processable by Selective Laser Melting (SLM). In addition, the use of critical raw materials such as rare earth metals should be avoided, and the alloy should be significantly cheaper than existing alternatives.
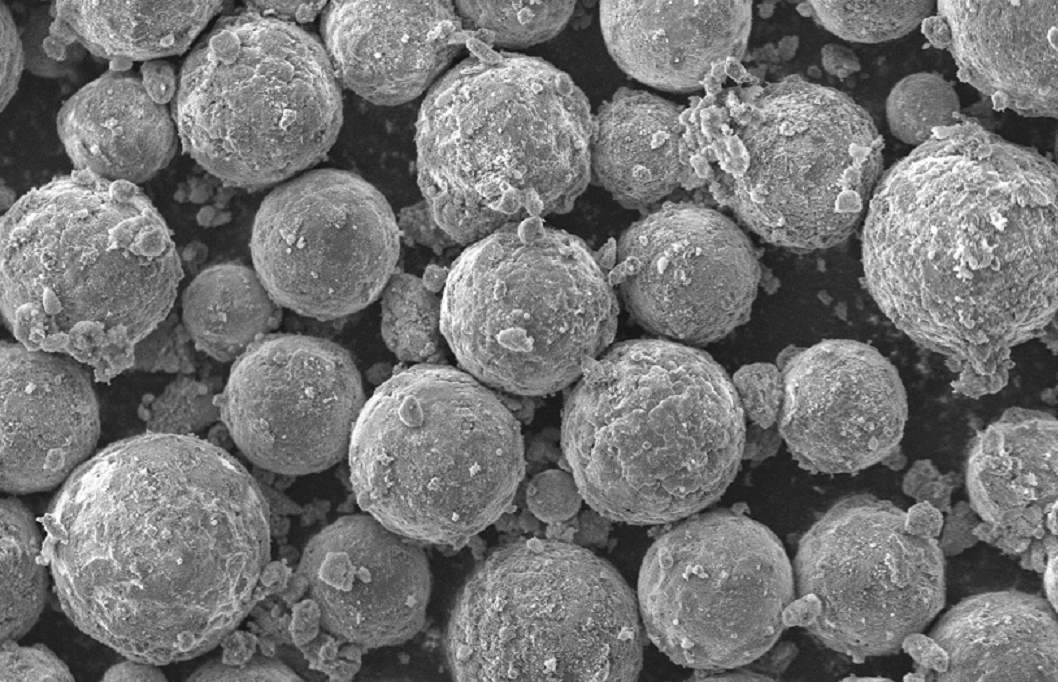
To consider the SLM process conditions with very small melt pool sizes, high temperature gradients and cooling rates, and with a cyclic heat treatment of the already consolidated material by succeeding laser scans, a combined process- and alloy simulation with ThermoCalc is used. This allows to estimate the formation of phases during the SLM process, and to optimize the material composition and powder production cycle appropriately.
Contacts: Chiara Monti, Dr. Konrad Papis
Achieving Material Circularity in High-Strength Aluminum Alloys for Additive Manufacturing
By using additive manufacturing (AM) technologies, such as laser powder bed fusion (LPBF) process, near net shape components can be manufactured limiting further tooling processes and thus reducing material waste. This is a key aspect since the feedstock materials involved, especially in LPBF of Al alloys, are expensive and critical from an environmental point of view.
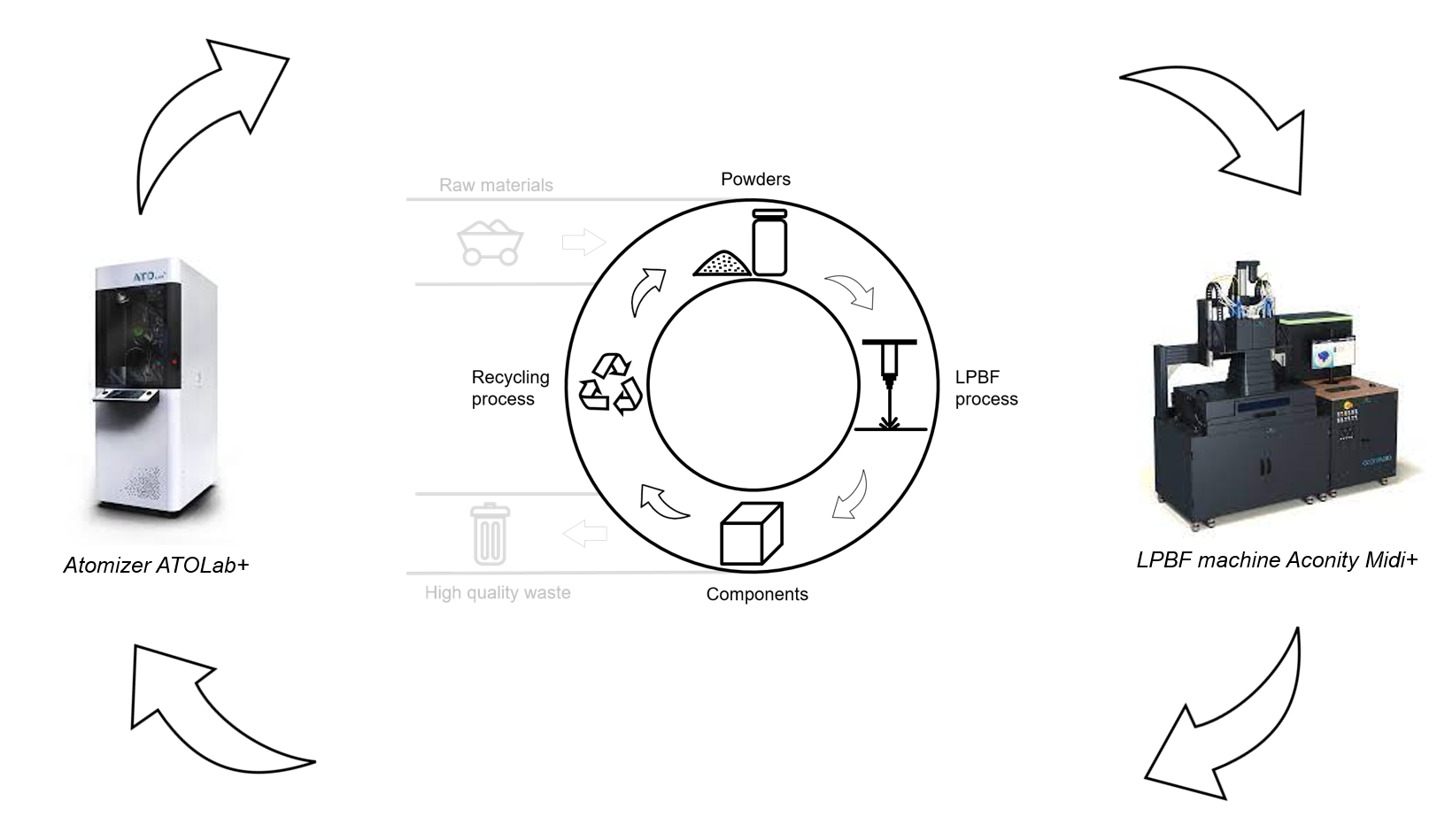
This work researches the possibilities and limitations for the recycling of LPBF-processed high strength Al alloys, which are subsequently re-processed into powders, and are re-used in LPBF. Components are manufactured using an Al-Mg-Sc alloy (Scalmalloy®), a promising high strength alloy, and then atomized, the powder attained is used to produce parts which are then compared to those made by virgin powder. Components and powders are characterized to evaluate changes in the chemical composition and the microstructural and mechanical properties. The same route is followed for a Ca-modified and for a Fe-modified Scalmalloy® composition and the influences of these alloying elements on the performances and on the recyclability of the alloy is investigated.
By this, the research contributes to a better understanding of sustainability aspects of laser-based AM processes, and will describe potentials for new and more sustainable Al-alloys for LPBF.
Contacts: Matteo Turani, Dr. Adriaan Spierings
Development of new aluminium alloy for Al-Metal Matrix Composites (MMCs) brake disc deposited by High-Speed Laser Cladding (HSLC)
The automotive industry is perpetually seeking advanced materials to enhance vehicle performance and efficiency. One of these key areas is brake disc technology, where the aim is to develop lightweight, yet highly wear-resistant solutions. For this, a new era of Aluminum-Metal Matrix Composites (MMCs) is emerging, utilizing High-Speed Laser Cladding (HSLC) as a sophisticated manufacturing method. Aluminum is an attractive base material for MMCs due to its light weight and good thermal conductivity. The integration of hard particles like Silicon Carbide (SiC) or Titanium Carbide (TiC) into the aluminum matrix further increases the wear resistance and hardness, making them ideal for brake discs. However, the development of these new alloys and the processing methods is complex. Porosity, crack formation, and uneven hard phase distribution can significantly impact the MMCs' mechanical properties and overall performance.

The HSLC process involves melting metal particles in-flight, which dramatically reduces the size of the melt pool and promises a more homogeneous distribution of reinforcement particles within the matrix. It also provides better control over cooling rates, which is vital for reducing cracking and porosity. Despite the promising results, further research is needed to better understand the compatibility of the matrix with hard phase particles and the influence of particle size on MMC properties. It's evident that the development of novel aluminum alloys tailored for HSLC can revolutionize the brake disc industry, bringing a new dimension of efficiency and performance to automotive engineering.
Contacts: external page Pauline Fichter, external page Dr. Konrad Papis