Directed Energy Deposition & Laser Cladding
Conventional and high-speed laser cladding (HSLC)
Laser cladding involves blowing powder (or mixture) into the process zone, where it’s molten by a laser beam to form a coating on a substrate. In High-Speed Laser Cladding (HSLC) the powder particles are molten in flight. This approach reduces heat input into the substrate, enabling the rapid and crack-free coating of dissimilar substrates, such as applying copper-alloy coatings on steel.
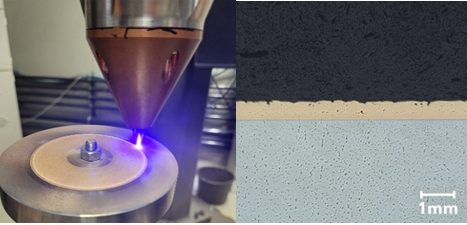
Applications:
• Tribological coatings such as bronze coatings for bearings, offering improved wear resistance and reduced friction.
• Hard coatings such as carbide coatings for brake discs, providing enhanced durability and performance.
• Specialty coatings including nickel-base alloys, cobalt-chromium base alloys, metal matrix composites, and non-ferrous metals for applications demanding corrosion resistance, hardness, or other tailored properties.
Research Interests:
• Process development for new alloys using infrared or blue lasers to achieve superior coating characteristics.
• Closed-loop control systems with active cooling to ensure optimal coating quality and consistency.
• Techniques for fabricating multi-layer and gradient materials, enable rapid alloy development and tailored material properties.
Contact:
external page Dr. Timo Schudeleit
Combined additive and subtractive manufacturing
Hybrid machines combine the best of two worlds. Material can flexibly deposited selectively and post-machining with the high accuracy and surface quality takes place on the same machine. Directed energy deposition (DED) is the only additive manufacturing technique, which works in 5-axis machines and allows for repair of components. The damaged surface is machined off, is build up additively and post-machines.

Applications:
• Repair of valuable parts (e.g. turbines)
• Net-shape manufacturing (e.g. compressors)
• Customization of casted parts
Research interests:
• Sensor integration for in-situ measurement and adaptive manufacturing (additive and subtractive)
• Distortion compensation (morphing)
• Exotic material deposition (cBN or carbide coatings)
Contact:
external page Dr. Timo Schudeleit
Process analytics and development
The laser and the powder stream build together the “tool” of a directed energy deposition (DED) machine. The process is with more than 25 parameters of high complexity. To define the optimal parameter set for a process, the tool and dependencies between parameters must be analysed carefully. This is done by advanced methods for measurement and profiling of the powder stream and the laser beam, as well as thermo-sensors for melt-pool monitoring and high-speed imaging.
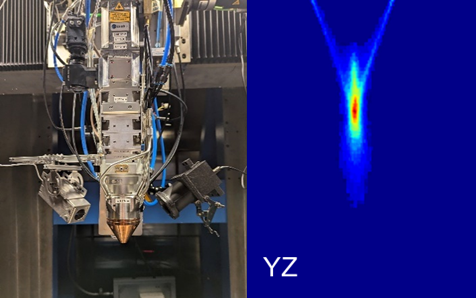
Applications:
• Detection of wear, instabilities and transient behaviour
• Process development for exotic materials or difficult-to-join materials
• Distortion prediction
Research interests:
• Increase of productivity and material efficiency in DED processes
• Optimized shielding for oxygen sensitive materials (e.g. titanium alloys)
• Quality improvement through controlled heat input
• Advanced monitoring for better control and insight into the cladding process.
• Coating characterization (e.g. adhesion testing)
Contact:
external page Dr. Timo Schudeleit