Laser Powder Bed Fusion
Metamaterial Structures via LPBF
Laser powder bed fusion enables the efficient production of complex structures with unconventional mechanical characteristics. Metamaterials are an example of this, where the local geometry is tailored to alter the gross physical behavior of the structure. With these, it is possible to create structures with amplified or attenuated acoustic or electromagnetic properties. One can also produce mechanically auxetic structures with a negative Poisson’s ratio or thermally auxetic structures with an effectively negative coefficient of thermal expansion. By combining multiple materials, it is possible to fabricate structures with directionally optimized structural and thermal properties.
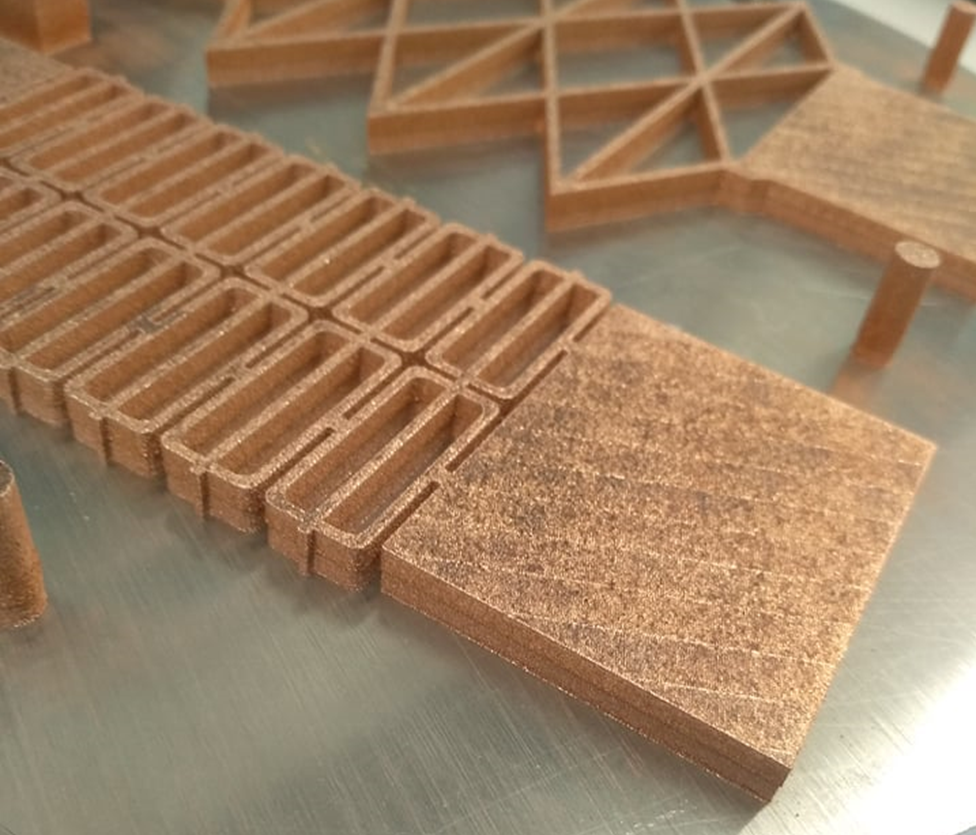
The realization of such structures requires specialized design and analysis tools. The complexity and fine dimensions of the local structures of the metamaterials requires advanced LPBF scanning techniques for producibility. We are also investigating the processability of multiple materials within a single build. Finally, the produced structures require laboratory characterization and validation that they achieve their design objectives.
Contact: Dr. Michael Tucker
Closed-loop Control of Laser Powder Bed Fusion
State-of-the-art laser powder bed fusion applications have a great room of improvement of stability and robustness due to complexity of thermal, mechanical and metallurgical phenomena acting on the process dynamics. With the increasing availability of process monitoring systems and advancements in data science, closed-loop control of the process has recently gained significant interest. Posing many challenges, the topic remains to be on the cutting edge of additive manufacturing.
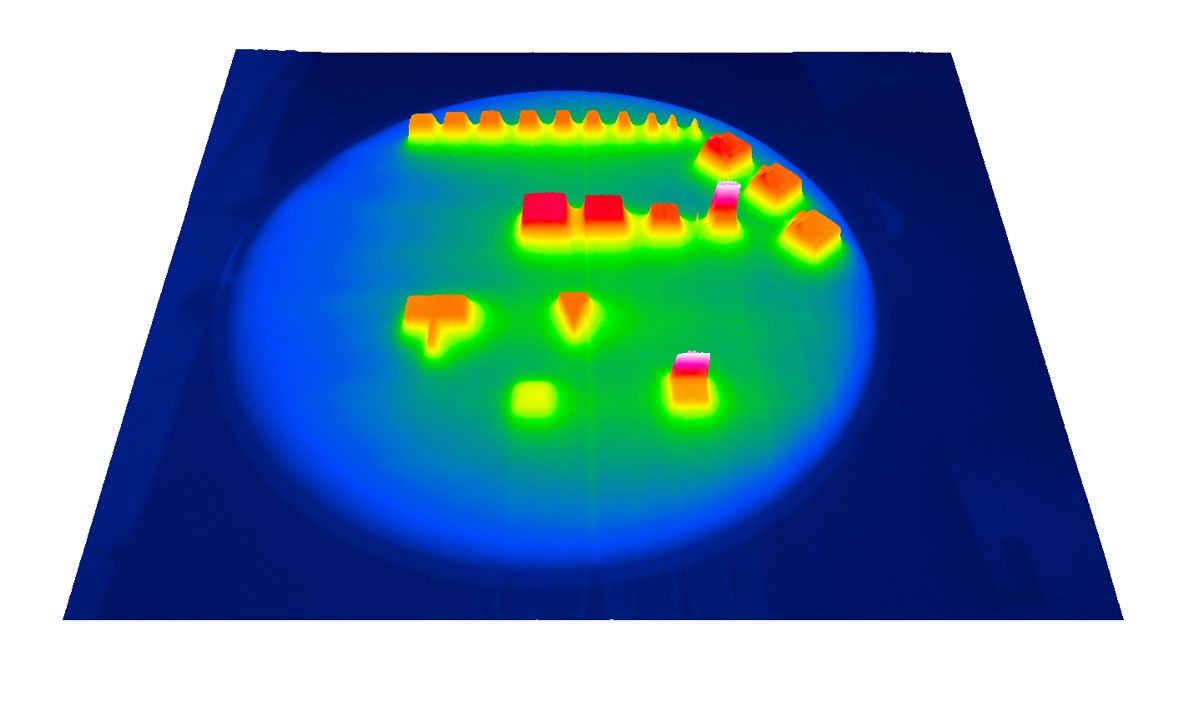
In this project, an additive manufacturing test bed equipped with in-line pyrometers and a high-speed CMOS camera, along with lateral powder bed monitoring camera and a thermal camera. By establishing a closed-loop control, collected sensor data are processed in situ in order to adjust the process parameters to stabilize the changing conditions. Project aims to increase the robustness of laser powder bed fusion process while enabling more complex geometries to be built.
Contacts: Baris Kavas, Dr. Michael Tucker
Computer vision for advanced LPBF quality control
State of the art LPBF systems operate with pre-defined process parameters and scan strategies. Due to the complexity of the process, and the interaction of the process with the part structure being built, the specific process manufacturing strategy affects the quality of the manufactured part. Thereby, many process imperfections can be observed visually. An advanced computer vision system coupled with machine learning is developed at inspire innovation centre for additive manufacturing, and integrated into a new adaptive process control to compensate process inconsistencies and heal manufacturing defects during the manufacturing process. For this, a new LPBF system is developed offering the required flexibility to integrate new monitoring solutions, and their integration into new control solutions.

Contact: Dr. Enrico Tosoratti, Dr. Adriaan Spierings