Multi-Material Processing
Multi-Material SPS
Additive manufacturing (AM) technologies for multi-material products from metals and ceramics are still in their infancy. In multi-material AM processes that melt powder or wire, miscibility issues, intermixing of liquid phases, interdiffusion and thermal stresses are issues to be dealt with. Materials with a large difference in melting point or immiscible materials are hard or impossible to process via melting-based AM processes. In this case, sintering and joining remain as options.
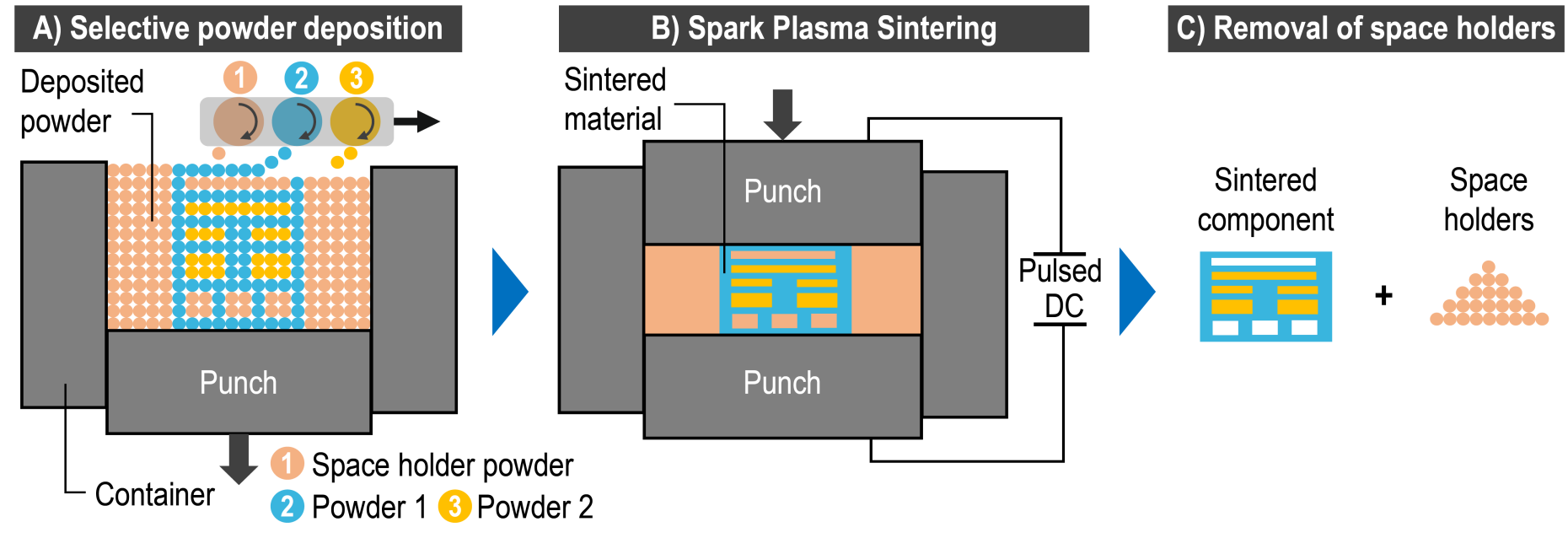
In this SNF funded project, an entirely new process for producing engineered 3D multi-material structures and components is proposed, which consists of binder-free selective powder deposition into a tool set and subsequent spark plasma sintering (SPS). This process can overcome the restrictions of existing technologies and allow for producing 3D multi-material structures at short process times and with materials that cannot be co-processed by melting. The proposed process raises new fundamental questions regarding the co-processing of different materials to defined 3D shapes. It is expected that the different electrical and thermal properties of the phases lead to an inhomogeneous temperature distribution, and that different resistances to compaction lead to inhomogeneous deformation. The specific goals of this project are i) to gain a scientific understanding of the densification behaviour during co-processing, ii) to develop methods for reducing incompatibilities between different powder materials and iii) to devise multi-phase multi-physics models for forward simulation of the process as well as optimal control and inverse methods for process design.
Due to the lack of knowledge about multi-material SPS of engineered 3D structures, this project focuses on three binary metal systems (Cu-Al, Cu-Ni, Cu-W) in order to reduce the metallurgical complexity. These material combinations are chosen based on their fundamental and technological interest, and because they are hard to process by melting-based AM processes. The expected impact of this research is a new process allowing for engineered 3D multi-material structures and products, especially from material combinations that are hard to process by melting-based AM processes, and new scientific knowledge of the co-compaction and co-sintering behaviour of three binary systems and suitable space holder material.
Contact: Dr. Léa Deillon, Marco Bernet
Multi-Material LPBF
Additive manufacturing processes such as LPBF allow complexity, individualization and weight reduction to be integrated into a design with only a marginal additional cost. The fabrication of multi-material parts by LPBF would yet further add the possibility to integrate functionality into a 3D printed component and thereby significantly extend the scope of application of the LPBF process.
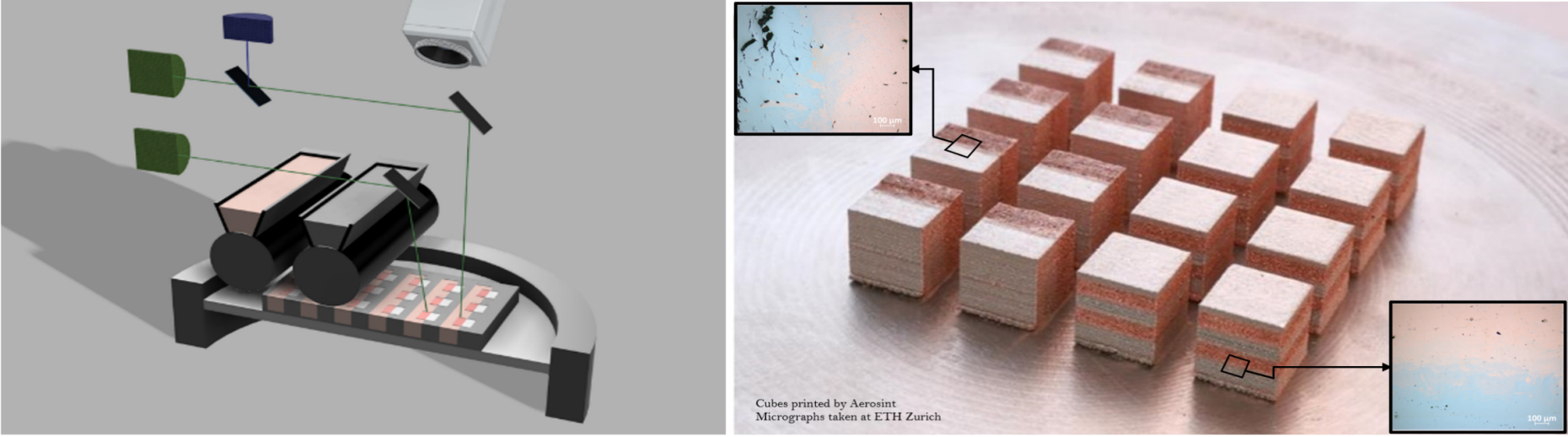
The Belgian company Aerosint recently developed a dual-material recoater that allows for deposition of two materials within a single layer in a voxel-like fashion. This recoater has been successfully used to produce Cu-steel parts. However, the mismatch in thermal and mechanical properties between the two materials makes it difficult to achieve defect-free interfaces and a strategy is needed to determine the optimal scanning path, scanning sequence, interfacial overlap and other process parameters. In a broader context, criteria need to be established to assess which materials properties are crucial in determining the co-printability of two materials and which level of incompatibility can be tolerated. This project is funded by the Strategic Focus Area “Advanced Manufacturing” and more information can be found here: https://www.sfa-am.ch/multi-mat.html
Contact: Dr. Léa Deillon, Caroline Pereira Martendal